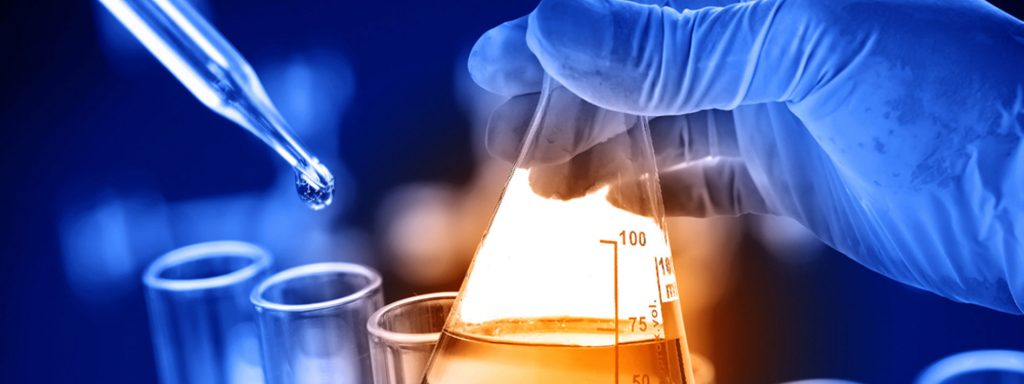
Hydraulic Oil Analysis
Through our flexible approach to supporting customers’ needs we can either supply sample kits for your in-house maintenance teams to take samples or our team of technicians can visit your site to obtain samples.
Hydraulic oil analysis is the same as having a blood test. Through an independent UKAS accredited laboratory (ISO 17025), OMS LubriTek will provide a diagnostic report on the condition of the oil. The report covers key areas such as ISO cleanliness level, ppm water contamination, wear metal contamination, TAN (oxidisation) and oil performance additive levels as these will deplete over time.
We will also provide a clear overview of all machines on site to accompany the individual diagnostic reports, which highlights the key findings and our recommendations of any oil management needs required to bring the oil back up to OEM specification requirements.
In addition to individual machine hydraulic oil analysis reports and machine overview report, OMS LubriTek can offer our customers access to an in-depth web based asset management system which enables users to closely follow hydraulic oil performance trends and condition monitoring on production machines. This is useful if you are having continuous issues with the same system and you want to carry out comparative tests with other machines to identify potential recurring problems and is also moving towards the next generation of oil management data logging.
Hydraulic oil analysis can also be introduced to companies working towards or to ISO TS16949, an ISO technical specification aimed at the development of a quality management system for continual improvement, emphasizing defect prevention in the automotive industry.
Sample Analysis Overview
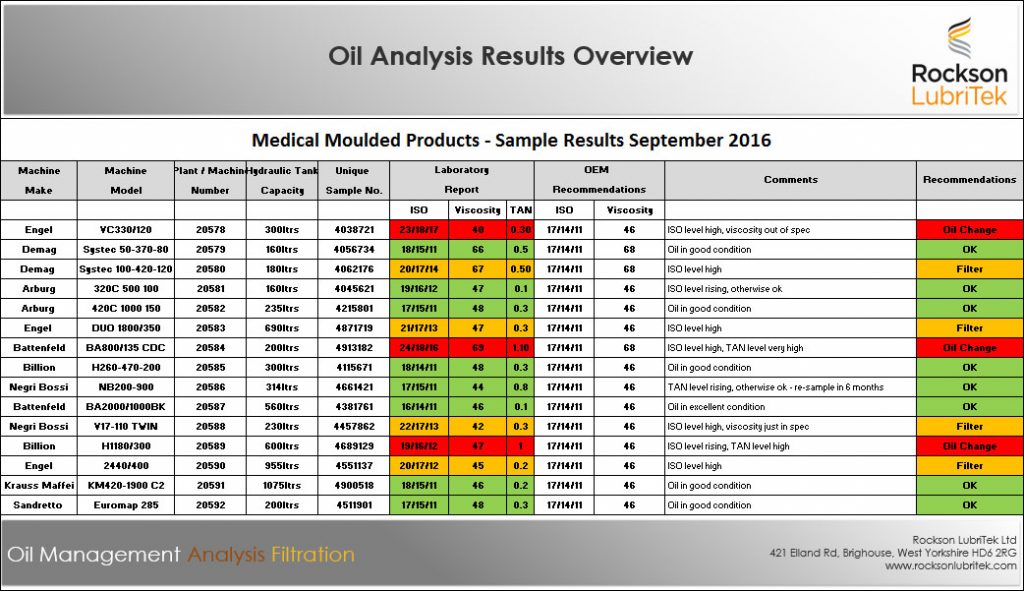